E10-SLAM(SLAM + DM Code Version)
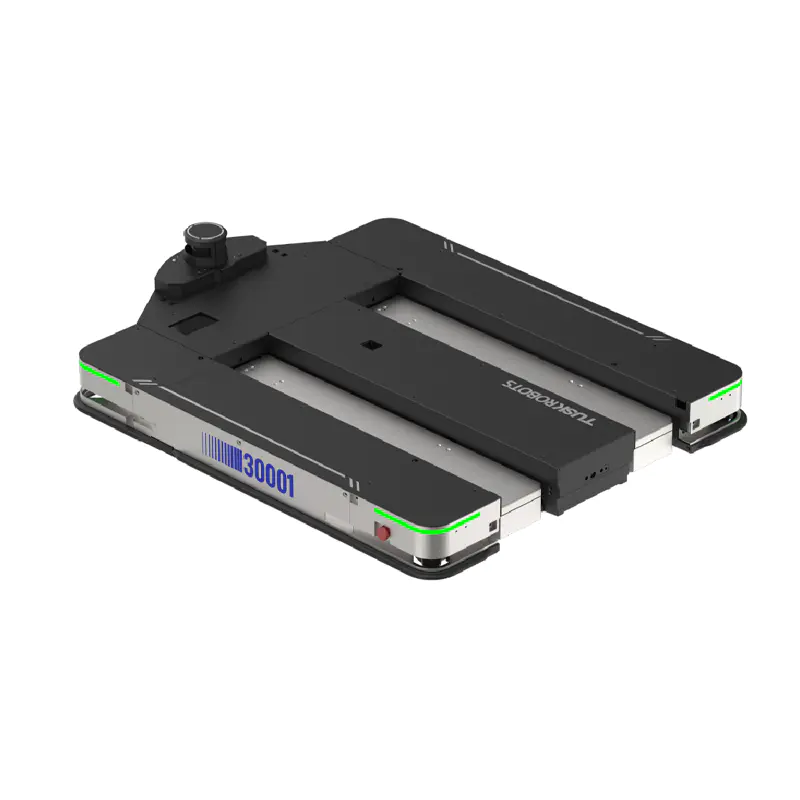
Project | SpecicCations | E10-SLAM(SLAM + DM Code Version) | |
---|---|---|---|
Basic Parameters | Size(mm) | 1399x1102x272.5 | |
Rated Load (kg) | 1000 | ||
Self-Weight (kg) | 320 | ||
Rotation Diameter (mm) | 1593 | ||
Fork Height (mm) | 90 | ||
Fork Stretch Out Max Limit (mm) | 1400 | ||
Fork Max Lifting Height (mm) | ≤330 | ||
Display Screen | 5 inches | ||
Telecommunication Modes | Default WIFl version: Support dual-band 2.4G/5G, IEEE802.11b/g/n (-5G version support 5G communication) | ||
Obstacle Avoidance Protection | Front laser sensors + Rear laser sensors, 360° obstacle avoidance detection | ||
Three-dimensional Protection | Forward-facing stereo camera visual obstacle avoidance | ||
Safety Protection | Detection Distance of Front Laser | ≤3m | |
Mechanical Protection | An emergency stop button, Reset button, A protection strip around The whole vehicle's body | ||
Caution Function | with voice and photoelectric alarm functions | ||
Navigation Mode | SLAM + DM code Dual Navigation | ||
Max Speed | 1.5m/s (Zero Loaded) / 1.2m/s (Fully loaded) | ||
Robot Stop Accuracy | ±10mm /±1° | ||
Movement Mode | two-wheel differential | ||
Maximum Robot Ground Adaptability | 40mm(Gap)/3.3°(Slope)/15mm(Stair-step) | ||
Maximum Fork Ground Adaptability | 10mm(Gap)/1.9°(Slope)/5mm(Stair-step) | ||
Lithium Battery Performance | Rated Voltage/Capacity | 51.2V/30AH | |
Battery Lite | The times of full charging: 2000 times (The battery capacity is guaranteed to be more than 70% of the new battery) | ||
Battery Endurance/Charging Time | ≥8H/≤2H | ||
Battery Type | LFP |
Specifications | Parameters | Types | |
---|---|---|---|
Inner Width of Slots W1(mm) | W1≤160 | ![]() |
|
Outer Width of Slots W2(mm) | W2≥600 | ||
Inner Pallet Height H(mm) | 95≤H≤130 | ||
Pallet Length L(mm) | ≤1400(DM Code Version) | ≤1300 (SLAM Version) | |
![]() |
As China Pallet Handling AGV manufacturers and Automated Guided Vehicle factory, Tuskrobots is committed to empowering intelligent logistics in smart factories, making handling simpler and more efficient.It has launched a globally unique and innovative intelligent robot product that is highly adaptable to international standard pallets for conveying and picking. Tuskrobots always insists on serving customers and pursuing customer value, sparing no effort to improve project delivery and after-sales service capability. We adhere to the customer-oriented concept with real actions, and we also continuously improve ourselves with customer feedback. To match customer usage scenarios and customer requirements, there are a variety of service products of Tuskrobots products and systems for customization or selection in the after-sales stage. Choose the service plan that suits you, we will provide service of high quality
Provide you with the latest enterprise and industry news
Provide you with the latest Industry knowledge about automated guided vehicle.
Pallet handling AGV (Automated Guided Vehicle) is a type of mobile robot that is specifically designed to transport palletized loads within a warehouse or manufacturing facility. These AGVs are equipped with sensors, cameras, and navigation systems that enable them to move autonomously along pre-defined paths or routes, avoiding obstacles and safely transporting materials.
Pallet handling AGVs can be programmed to follow specific routes to pick up and deliver pallets of materials to designated locations within a facility. They are also capable of interacting with other machines and equipment, such as conveyors and lifts, to efficiently move materials around the facility.
Using pallet handling AGVs can significantly improve the efficiency and productivity of a warehouse or manufacturing facility. They can operate 24/7 without breaks, reducing downtime and increasing throughput. Additionally, they can reduce the need for human intervention in the material handling process, which can improve safety and reduce labor costs.
Automated Guided Vehicles (AGVs) have become an increasingly popular solution for material handling in industries such as manufacturing, warehousing, and distribution. Here are some of the advantages of using AGVs in material handling:
1. Increased Efficiency: AGVs can operate 24/7 without the need for breaks or rest, which can significantly increase the efficiency of material handling processes. Additionally, AGVs can be programmed to optimize their routes and schedules, reducing the time required to move materials from one location to another.
2. Reduced Labor Costs: Implementing AGVs can reduce the need for human intervention in the material handling process, which can result in significant labor cost savings. With AGVs handling the transportation of materials, workers can focus on higher value tasks, such as quality control and process improvement.
3. Improved Safety: AGVs can improve safety in material handling operations by reducing the risk of accidents caused by human error. AGVs are equipped with sensors and safety features that allow them to navigate around obstacles and avoid collisions with other equipment and workers.
4. Flexibility: AGVs can be programmed to perform a wide variety of material handling tasks, such as palletizing, depalletizing, and transporting goods. They can also be easily reprogrammed to adapt to changing production requirements and facility layouts.
5. Space Optimization: AGVs can operate in areas with limited space, such as narrow aisles and tight corners, which can be difficult or impossible for other types of material handling equipment to navigate. This can help maximize the use of available floor space and increase storage capacity.
6. Data Collection and Analysis: AGVs can be equipped with sensors and software that allow for real-time data collection and analysis, providing insights into material flow and process performance. This information can be used to optimize production schedules, identify bottlenecks, and improve overall efficiency.
In conclusion, using Automated Guided Vehicles in material handling operations can offer significant advantages, including increased efficiency, reduced labor costs, improved safety, flexibility, space optimization, and data collection and analysis.
Robotics technology has transformed the way manufacturing and warehousing operations function. With the advancement of robotics technology, many processes can now be automated, making it possible to improve efficiency, accuracy, and safety. Here are some common applications for warehousing robotics in manufacturing and warehousing:
1. Palletizing and Depalletizing: Robotic palletizers can automatically stack and arrange products onto pallets, while depalletizers can automatically remove products from pallets. This process eliminates the need for manual labor and increases the efficiency of material handling.
2. Order Picking: Robotics technology can be used to automate the order picking process by using robotic arms or autonomous mobile robots (AMRs) to pick and transport products to the shipping area. This process can improve the accuracy of order picking and reduce the time required to fulfill orders.
3. Packaging and Labeling: Robotic technology can be used to automate the packaging and labeling process by using robotic arms to package products and apply labels. This process can reduce the risk of damage to products during packaging and increase the speed of the packaging process.
4. Sorting and Conveyor Systems: Robotics technology can be used to automate the sorting and conveyor systems by using robots to transport products along the conveyor belt, sort products by weight, size, or other characteristics, and direct products to the appropriate location.
5. Inventory Management: Robotics technology can be used to automate the inventory management process by using robots to count inventory, track inventory movements, and locate products in the warehouse. This process can improve inventory accuracy and reduce the time required for inventory management tasks.
6. Inspection and Quality Control: Robotics technology can be used to automate the inspection and quality control process by using robots to detect defects, measure dimensions, and identify non-conforming products. This process can improve the quality of products and reduce the risk of defects.
In conclusion, robotics technology has many applications in manufacturing and warehousing operations, including palletizing and depalletizing, order picking, packaging and labeling, sorting and conveyor systems, inventory management, and inspection and quality control. These applications can help to improve efficiency, accuracy, and safety in these industries.
Automated Guided Vehicles (AGVs) are a versatile technology that can help to maximize efficiency and productivity in material handling processes. Here are some strategies for maximizing the benefits of AGVs in your facility:
1. Identify the Right Applications: AGVs can be used in a wide range of material handling applications, from simple transport tasks to more complex operations like palletizing and depalletizing. Identifying the right applications for AGVs in your facility can help to ensure that they are being used to their fullest potential.
2. Optimize Your Layout: The layout of your facility can have a significant impact on the efficiency of material handling operations. AGVs can be programmed to navigate complex layouts and optimize their routes to minimize travel time and maximize throughput. Careful planning and optimization of your facility layout can help to further increase the efficiency of AGVs.
3. Streamline Your Processes: AGVs can be integrated with other material handling equipment, such as conveyors and robotic arms, to further streamline your processes. This can help to reduce cycle times and increase productivity.
4. Ensure Proper Maintenance: Like any other equipment, AGVs require regular maintenance to operate at peak performance. Regular inspections, cleaning, and preventive maintenance can help to reduce downtime and extend the lifespan of your AGVs.
5. Implement Real-Time Monitoring: Real-time monitoring of AGVs can help to identify issues and inefficiencies in your material handling processes. This information can be used to optimize routes, adjust schedules, and identify areas for improvement.
6. Train Your Staff: Training your staff on how to work effectively with AGVs can help to maximize their efficiency and productivity. This can include training on how to program and monitor AGVs, as well as how to work safely in a facility with AGVs.
In conclusion, AGVs can help to maximize efficiency and productivity in material handling processes. To fully leverage the benefits of AGVs, it’s important to identify the right applications, optimize your facility layout, streamline your processes, ensure proper maintenance, implement real-time monitoring, and train your staff. With these strategies in place, you can help to create a more efficient and productive material handling operation.